Rapid Prototyping with 3D Printers
- Admin
- Nov 9, 2017
- 3 min read
A key step in any engineering project is delivering proof of concept. Whether it’s a circuit board for a new technology or a conceptually unique mobile device case, at some point a sample must be delivered that proves the viability of the product. In days of yore, the prototype may be a model made from paper, foam, or milled from wood or metal. These may be high quality, but you often pay for that quality in time or money, a luxury not all of us can afford. Enter 3D printing, an emerging technology that adds speed and convenience to the prototyping phase.
With a 3D printer we can start practicing “rapid prototyping.” Rapid prototyping is a practice of producing prototypes with short iteration time. Makes sense, huh? Rapid prototyping is also a feedback loop. Design, as we all know, is an iterative process, and the rapid prototyping methodology is no different. The loop is simple: design, print, test/assess, revise, repeat.
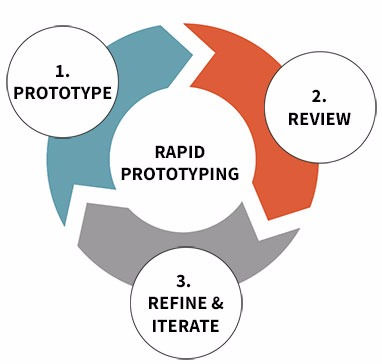
The fun begins here. For our purposes, design encompasses concept ideation, any initial drawings or renderings, and creation of a 3D model. The 3D model is the end goal here. For the first specimen, it is acceptable to aim for minimal viable product (MVP). MVP provides only the basic solutions of the final product. For our loud cell phone case, we needed just that and nothing more – a phone case that made the speaker louder with no extra features.
This step in the cycle is self-explanatory. The printing step is simply making the part with your 3D printer or through a 3D print service, like Sculpteo, 3D Hubs, or Protolabs (Sondare has no affiliation with any of the above, these are simply 3 well-known services). Anyone who has operated a 3D printer before knows that it is not a perfectly simple process, as there is much that can go awry in the print, but the point here is to get a physical model in your hand, quickly. Note: different 3D slicer programs will offer different compatibility for various 3D file types, so keep that in mind when exporting the file.
Test/Assess
Here we assess the viability of the part. This may be as simple as holding it in your hand to inspect the form factor, or it may involve rigorous testing. In the development of our acoustically enhanced cell phone case, we took the printed part and checked it for fit and tested the acoustics in our sound room. 3D printed parts are often of a lower cosmetic and physical fidelity than a finished product, so the testing should take that into account. That is, if testing for strength, one needs to scale the requirements of the test to the ability of the printed part. We initially only tested the acoustic attribute of the case, so our printer material, PLA, was acceptable.
Revise
After we test or otherwise assess our part, we begin the cycle anew with changes in mind. Any changes can quickly be made to the model, another print can begin, and another round of testing will commence. With luck, this cycle of revisions may only last a few iterations, or it can go on for dozens more. Our mobile case project took a few months of iteration to hone in on the correct fit, smooth frequency response, proper volume boost and other attributes and features. A few months may sound like a long time for a phone case, but without our 3D printer going to work every day, we either would have had to settle on a design lacking certain physical features or having an inadequate sound profile.
For example, our phone case developed a more ergonomic feel during product development. As we created samples and handled and tested them, there were certain points of contact that were too sharp or uncomfortable. Any consumer product, especially a well-handled product, needs to be comfortable for multiple users, so we fixed these in our revision process by replacing them with round edges. This and many other changes were able to be incorporated quickly through the rapid prototyping process.
The rapid prototyping process has key advantages over traditional prototyping processes. First, it saves time. The only limit on your speed is the 3D printer, and today’s printers can produce parts faster than ever before. Second, it saves money. Once the initial investment in the printer is made, 3D printing is incredibly cheap. Material is as low as $15/kg and there is no wage-earning operator, far undercutting the price of a CNC-machined part. It is also possible to experiment with more variability in different components of the product. Different customers may have different requirements, so the ability to test small changes quickly helps deliver the final product faster.
Rapid prototyping, aided by the rise of 3D printers, allows shorter lead times and less expensive product development. It has been indispensable to Sondare Acoustics and it can surely be incorporated into any company’s plans.
Komentar